Are you constantly tangled up in inventory tracking or feel like managing your rental items could be smoother? If so, it might be time to consider whether a barcode system is right for your business. Implementing a barcode system can streamline operations, dramatically reduce human error, and free up time for you to focus on expanding your business and enhancing customer service.
So, should you implement a barcode system for your rental business? Absolutely, if you’re looking to boost efficiency and accuracy in your operations. Whether you rent audio equipment, party supplies, or heavy machinery, barcoding each item can help you manage your inventory precisely and easily.
Let’s dive into how a barcode system can transform your business, making tracking and managing your rental items easier.
Understanding Barcodes
Barcodes are black-and-white lines or patterns that help computers quickly and accurately identify items. When you scan a barcode with a reader, the device translates the barcode into a number or string of characters, which is often referred to as a serial number. Here’s how the process works:
- Generating Serial Numbers: Businesses create or generate serial numbers that they assign to their inventory. Serial numbers may be assigned to individual units of a high-value item type, like tractors or a single serial number might be used to account for many low-value items, like linens or cutlery.
- Assigning Barcodes: The assigned serial numbers are then linked to barcodes. These barcodes are printed and attached to the inventory items.
- Scanning Barcodes: A barcode scanner is used to read the barcode, translating it back into the assigned serial number. In this way, a barcode scanner functions similarly to a keyboard, reading the information in the barcode and inputting it into a database automatically.
This information is matched with details in the database, such as price, quantity, or description, making inventory management much more efficient.
Do All Barcodes Work The Same?
Not all barcodes are the same. They come in different types, designed for various uses based on the amount of data they can hold and how they are scanned. The two main types are:
- 1D Barcodes: These are the traditional barcodes you often see on grocery items and are also called linear barcodes. They use spaces and bars of different widths to encode information which is generally numerical. 1D barcodes are great for general purposes but can only hold up to 85 characters.
- 2D Barcodes: Unlike 1D barcodes, 2D versions can include more information and use a matrix of dots, squares, and other shapes. Common examples are QR codes. They can hold a wide range of data, including numbers, text, and URLs, and can store up to 2,000 characters. This makes them useful for more complex applications like storing web links, addresses, or multiple pieces of data about an item.
When Should You Use 1D and 2D Barcodes?
1D barcodes are typically used in retail for managing inventory and sales because they are quick to scan and simple to implement. These are best used for cases where you only need to track a product name, quantity, or price.
On the other hand, 2D barcodes are useful in environments where more information needs to be stored or where space is limited. They are commonly used in marketing for linking to websites, and in operations to provide detailed shipment information or to track items through the order process.
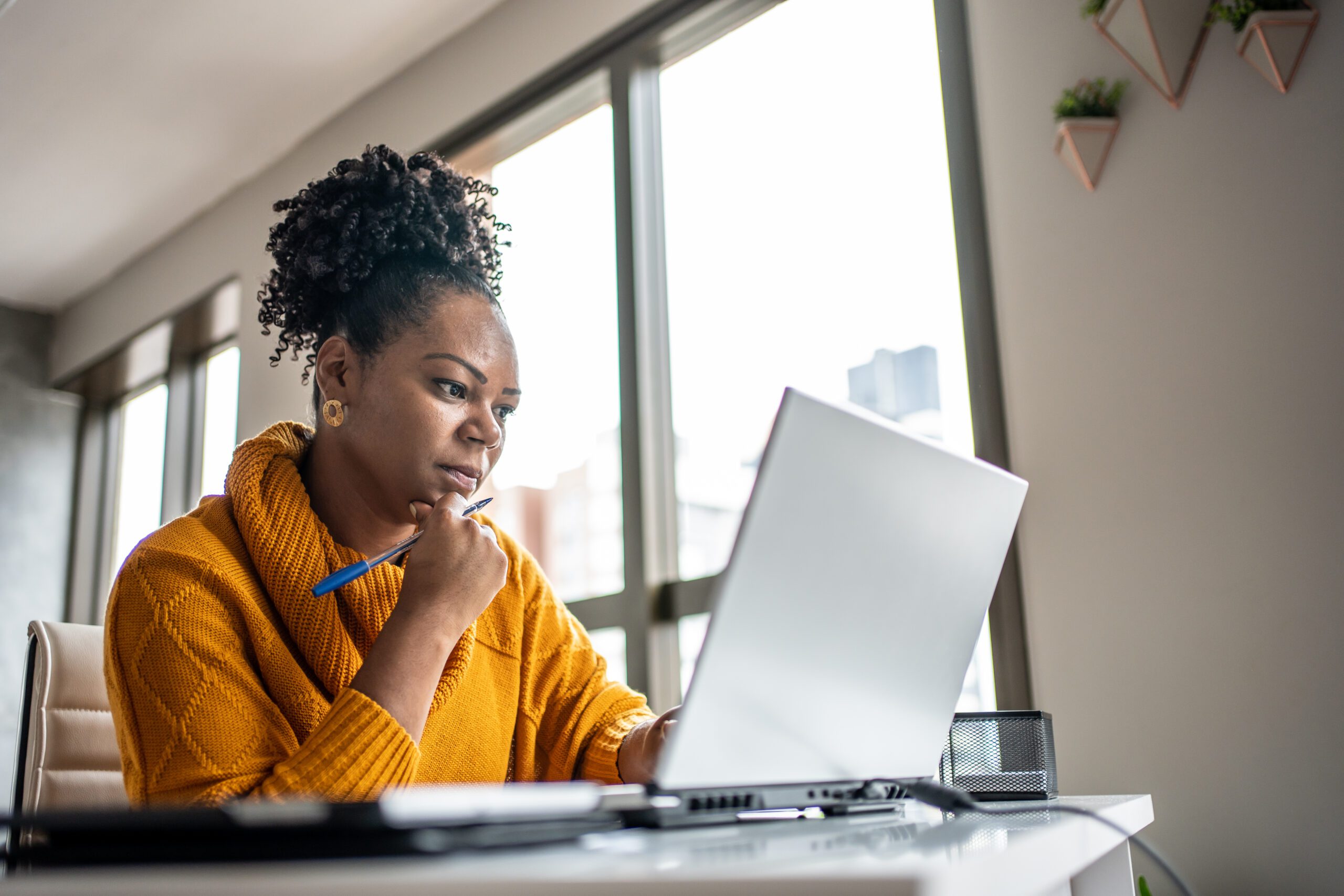
Why Rental Businesses Should Barcode Inventory
Now that you understand what barcoding is and why it’s used, you might be asking, “Okay, but why should I implement barcoding in my rental business?” Changing your operations is indeed a big step, and tagging all your inventory takes time.
If your business is running smoothly, or if you’re pressed for time, you might hesitate to start this process. However, the advantages of using a barcode system greatly outweigh the initial time investment for these reasons:
- Speed and Efficiency: Barcoding speeds up the check-in and check-out processes. You can handle transactions much faster, which means less waiting for your customers and quicker turnovers for your equipment.
- Accuracy: With barcodes, you’re less likely to face errors during transactions. Accurate tracking reduces the chances of mix-ups or losses, which can save you a lot of headaches and keep your customers happy.
- Inventory Control: Barcodes give you real-time data on what’s in stock, what’s out on rent, and when it’s due back. This means you always know where your items are, which helps prevent overbooking and ensures you meet customer demand.
- Cost Savings: By reducing errors and improving efficiency, you also cut down on costs. Less time spent fixing problems means more time spent growing your business.
Implementing a barcode system might seem daunting at first, but the long-term benefits make it worthwhile for your rental business.
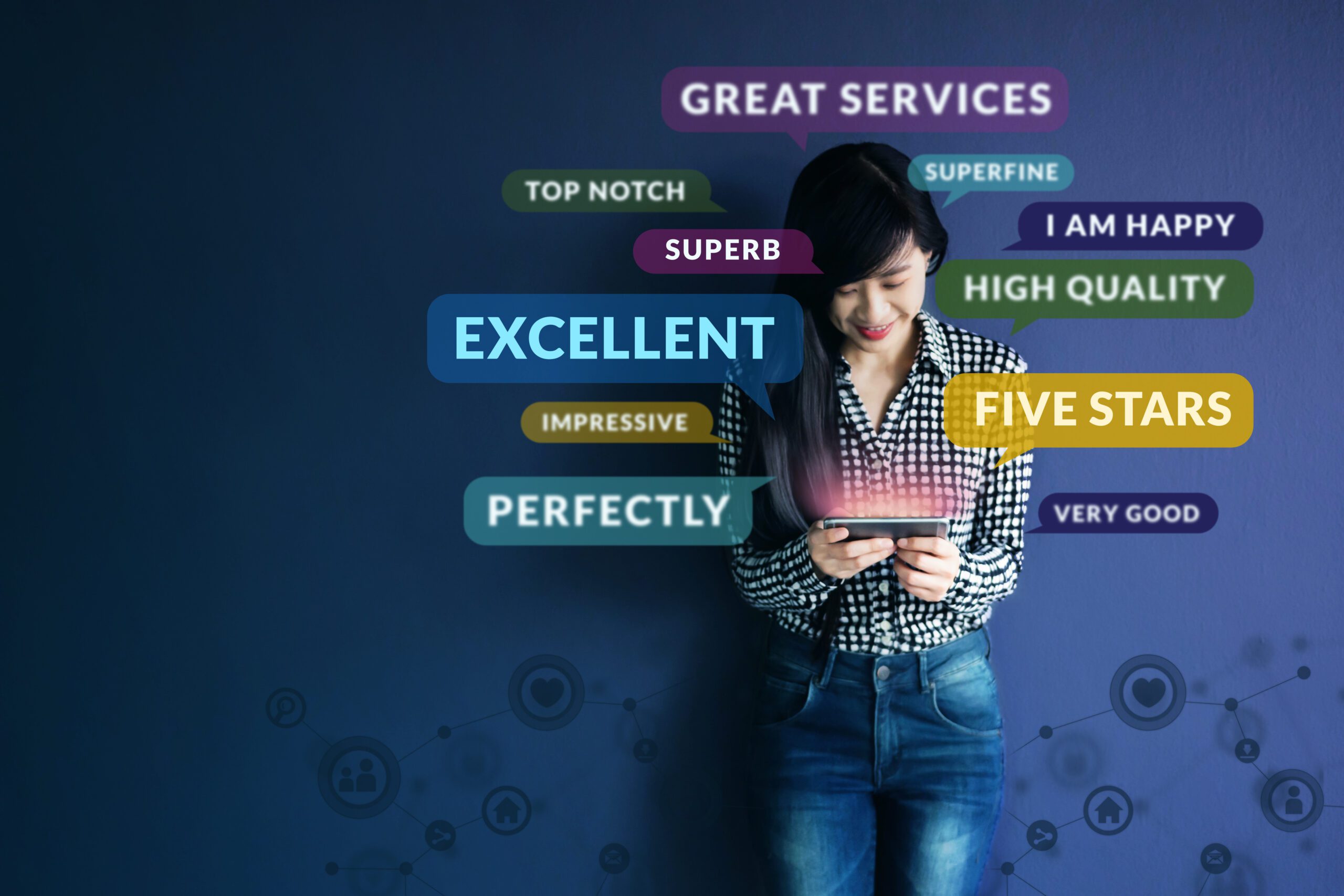
Setting Up A Barcode System
Implementing a barcode system can streamline your operations, improve inventory management, and enhance customer service. Here’s a step-by-step guide on how to set up a barcode system for your rental business!
1. Choose the Right Barcode Type
Decide whether 1D or 2D barcodes will best suit your needs. 1D barcodes are sufficient for basic inventory tracking, such as checking items in and out. If you need to store more information or want to use the barcodes for marketing purposes (like QR codes linked to promotional content), consider 2D barcodes.
2. Create Your Serial Numbers
Serial numbers are unique identifiers given to items in your inventory. They help you keep track of each specific item, whether it’s a large piece of equipment or a set of linens. A typical serial number might have a mix of letters and numbers, such as ABC12345. This format helps keep each number distinct and easy to read.
Some rental software can automatically generate serial numbers for you. This is a big help because it ensures that each number is unique and saves you time. When you add a new item to your inventory in the software, it creates a serial number for that item without you having to do anything.
Serial numbers are crucial for tracking each item in your inventory. They help you see which items are rented out, which are available, and when items are due back. This makes managing your inventory a lot smoother and helps prevent mix-ups with items that might look similar.
Here are some good rules to follow when creating serial numbers:
- Use the same format for all your serial numbers. This makes it easier to manage and understand your inventory.
- Begin serial numbers with letters that indicate the type of item. For example, use “TENT” for tents and “CHR” for chairs. This helps you quickly identify what the item is just by looking at its serial number.
- Ensure your serial numbers are long enough to stay unique but not so long that they’re hard to use. Usually, six to eight characters are enough.
3. Purchase Barcoding Hardware
If you plan on using barcodes to track your inventory, a scanner is nonnegotiable. Here are some criteria you can use to pick the best scanner for your needs:
- Ensure the barcode system is compatible with your existing inventory software. It should easily integrate without needing to change much of your current processes.
- Choose scanners and software that are user-friendly, especially if your team is not very tech-savvy. Simple interfaces and clear instructions will help reduce training time and errors.
- Consider the environment in which the scanners will be used. If your inventory is stored in large warehouses, you might need scanners with a longer range. For rough environments, look for durable scanners that can withstand falls or harsh conditions.
- Determine which type of barcode is suitable for your needs. For instance, 1D barcodes are common for general items, while 2D barcodes can store more information. Decide which one you will use, and make sure your scanner is compatible.
By following these guidelines, you can choose a barcode system that enhances your inventory management, making your operations smoother and more efficient.
4. Generate and Print Barcodes
When it comes to generating and printing barcodes, you have a couple of options. You can either use a service to purchase high-quality barcode labels or invest in a barcode printer. Both methods have their advantages:
- Purchasing barcode labels from a professional service can ensure that you get durable, high-quality labels. This is especially helpful if you don’t want the hassle of printing them yourself.
- If you have a lot of items or find yourself frequently adding new inventory, buying a barcode printer might be a good investment. This allows you to print barcodes as needed and can be more cost-effective in the long run.
Whether you decide to use a service or print barcodes yourself, here are some best practices to ensure your barcodes work well and last long:
- Make sure the barcode is large enough to be easily scanned but not so big it takes up too much space on your item. Typically, a barcode should be about an inch wide.
- Barcodes are most often printed in black on a white background. This high contrast helps ensure that barcode scanners can read them easily.
- If your items are used outdoors or handled frequently, choose labels that are waterproof and tear-resistant. This ensures that the barcode stays readable throughout the life of the item.
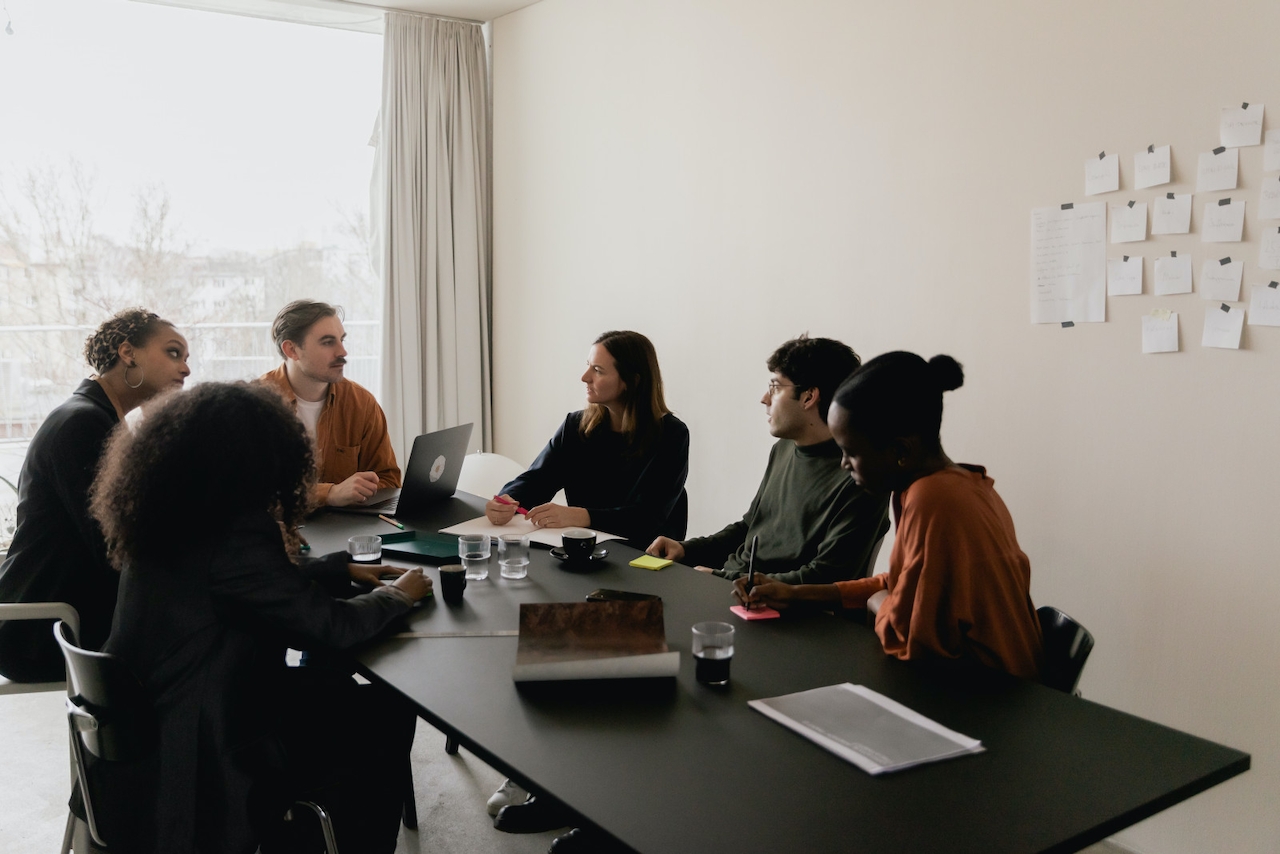
5. Label Your Inventory
Properly placing barcodes on your inventory is key to ensuring they are effective and help streamline your operations. Here are some best practices for labeling your inventory with barcodes, along with examples of where to best place them on different types of items.
- Choose a Consistent Location: Always place barcodes in the same general location on similar types of items. This consistency speeds up the scanning process because your staff will know exactly where to look.
- Ensure Visibility and Accessibility: Place barcodes where they can be easily seen and scanned. Avoid locations that require moving the item or getting into awkward positions to scan.
- Avoid High-Wear Areas: Keep barcodes away from areas that are likely to get worn out or dirty. This helps ensure that the barcode remains scannable throughout the life of the item.
- Use Protective Covering: For items that are used outdoors or in rough conditions, consider using a clear protective overlay to protect the barcode label from damage.
Best Barcode Placement for Common Items
Item Category | Placement of Barcode |
---|---|
Tables and Chairs | Place the barcode on the underside of the tabletop or a non-visible part of a chair leg. |
Power Tools and Equipment | Attach the barcode on a smooth, flat surface that doesn’t interfere with the use of the tool. Avoid grips or moving parts. |
Tents and Large Fabrics | Attach the barcode to the storage bag or on a tag sewn into a seam, where it won’t interfere with setup or take-down. |
Sound Equipment and Electronics | Place barcodes on the back or bottom of the equipment, ensuring it does not block vents or interfaces and is on a flat area for easy scanning. |
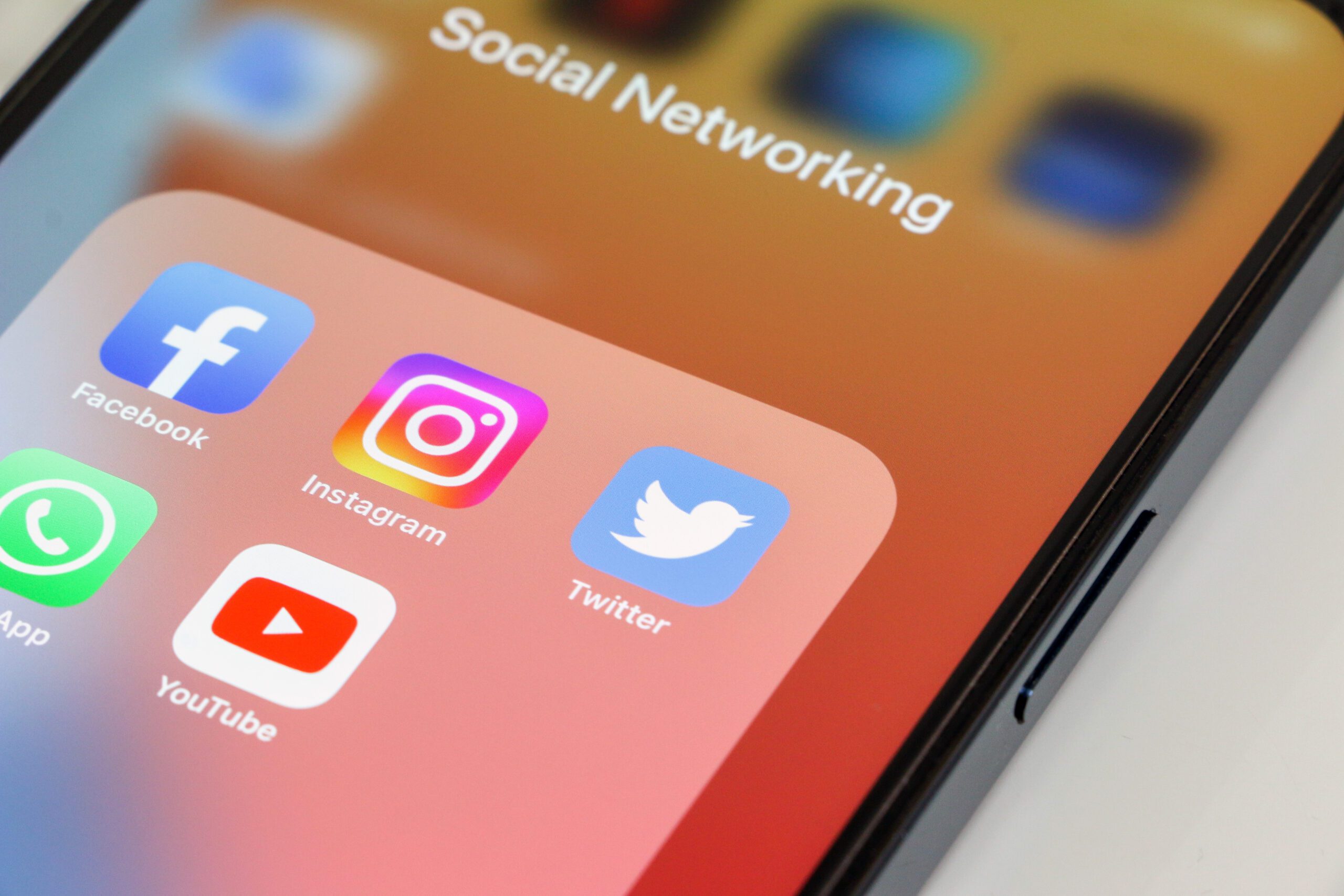
So, Do Rental Businesses Need A Barcoding System?
“Need” is a strong word. Will barcoding your inventory make or break the success of your business? Not necessarily. If you don’t implement a barcoding system, your business isn’t doomed to fail. However, it’s important to recognize that barcoding your inventory can significantly impact your operations in positive ways, leading to smoother processes and higher profits.
Implementing a barcoding system can streamline how you manage your inventory, making it faster and more accurate. This means less time spent on manual checks and more time available for focusing on other important areas of your business, like customer service and growth initiatives.
While a barcoding system may not be an absolute necessity for every rental business, the benefits it offers make it a worthwhile investment. By reducing errors, saving time, and improving efficiency, barcoding can help take your business to the next level. If you’re aiming to make operations more efficient and boost profitability, then a barcoding system should definitely be on your radar.
Other blogs you may find helpful:
5 Reports that Rental Businesses NEED to Review Frequently
The Importance of Equipment and Party Rental Contracts in 2024
A Step by Step Guide to Becoming a Preferred Vendor at an Event Venue
Frequently Asked Questions
Barcoding refers to the use of barcodes to automate the tracking and management of inventory. Barcodes are black-and-white patterns that scanners read to retrieve information about items quickly. This system streamlines processes such as check-in, check-out, and inventory audits, making them more efficient and less prone to error.
Small businesses can create a barcode inventory system by following a few straightforward steps. First, generate unique serial numbers for each inventory item. Then, use barcode software to create barcodes that represent these serial numbers. Finally, print these barcodes on labels and securely attach them to the respective inventory items, ensuring each item can be quickly and accurately identified and tracked through its barcode.
Yes, a small business can create its own barcode system by purchasing or subscribing to barcode generation software, obtaining the necessary scanning hardware, and integrating this system with the business’s existing inventory management software. It involves setting up the hardware (scanners and/or label printer), designing and printing the barcodes, and training staff on the new system.
Barcoding systems work by encoding data into visual patterns (barcodes) that a scanner can read. When a barcode is scanned, the scanner translates the patterns into digital data—typically a serial number—that is then matched with information in a database. In this way, a barcode scanner functions similarly to a keyboard, reading the information in the barcode and inputting it into a database automatically.
To set up a barcoding system, you’ll need several essential components. First, barcode software is crucial for generating and managing barcode data, creating unique serial numbers that are encoded into each barcode. You also need a barcode scanner to read the barcodes and translate the encoded information into digital data. Additionally, you’ll need appropriate labels and supplies for printing and securely attaching barcodes to your items.